Research
The FASER Lab is dedicated to novel approaches to solving robotics issues centered around the question:
“HOW CAN A MULTI-AGENT ROBOTIC SYSTEM OPTIMALLY USE ITS CAPABILITIES TO ENSURE THE ROBUST COMPLETION OF TASKS IN THE FIELD?”
Variety
In-space applications require robots to fulfill a variety of functions and to be able to handle the construction and manipulation of various types of spacecraft components including:
Support Trusses | Instruments | Reflectors | Solar Arrays
Harnesses | Propulsion Units | Radiation Shields | Habitat Modules
In construction, robots must be efficient and low maintenance, while being able to join components with a high degree of rigidity.
Distribution
Purpose-built solutions function excellently for work in a controlled repeatable setting. However, space is none of these things. Space assembly robots must be modular and distributed to be economically viable. This means that they must be able to perform a wide variety of tasks while remaining cost efficient and resistant to failure.
Assembly of any kind requires object manipulation – typically assembly components or tools. Generally, assembly robots can be categorized as either serial manipulators or parallel manipulators. Serial manipulators are comprised of a series of rotational and prismatic joints and actuators, generally configured to give the robot 6 degrees of freedom. These types of robots are generally what is considered a robotic arm. Serial manipulators have a comparatively large reach but sacrifice payload capacity and stability. Parallel manipulators are comprised of a series of prismatic and rotational actuators which are configured in parallel such that anywhere between 3 and 6 (6 being most common) actuators are connected between the top and bottom of the robot. This type of robot is generally referred to as a Stewart platform.
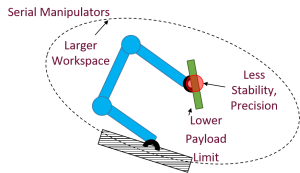
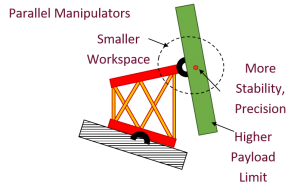
Parallel manipulators have a very small effective workspace, especially compared to serial manipulators, but make up for it in their resistance to back-driving, formidable strength, and high rigidity.
From a controls standpoint, serial and parallel manipulators differ considerably. Inverse kinematics – determining the position of joints from the position of the end effector of a robot – is generally the harder problem to solve, while forward kinematics – determining the position of the end effector from the position of the joints – tends to be easier. While this is true for serial manipulators, the opposite is true for parallel manipulators, as inverse kinematics is generally used to drive the robot, while forward kinematic solutions are generally imprecise and multiple solutions can be found.
Autonomous space assembly depends on the distribution of tasks to the smallest individual element. The comparative strengths and weaknesses of serial and parallel manipulators enable collaboration, with serial manipulators providing large scale movements, while parallel manipulators provide fine-tuning and delicate manipulation tasks. Examples of this type of collaboration include NASA Langley’s NINJAR and LSMS experiments, as well as the IPJR solar array construction demonstrations.
Estimation
As more elements are introduced into a system, the chance for failure increases. Constructing spaceborne macrostructures out of base materials will certainly introduce potential for failure into the system, especially in cases where structures are being built using fixed jigs. Jigs without the ability to adapt to changing situations will cause assembled structures to inherit any biases present in the jig and propogate them throughout the system.
Using maximum likelihood estimation (MLE) and appropriate filters, such as Kalman filters, robots can detect errors in a structure it is building and dynamically adapt to compensate. In the NASA Intelligent Jigging and Assembly Robot (NINJAR) (pictured below) truss assembly demonstration, the system examined the global positions of strut objects relative to each other and commanded NINJAR to reposition itself until all errors were sufficiently mitigated for welding the truss together.
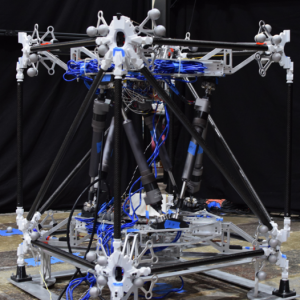
Sequencing
Traditional robotic assembly processes, such as the standard assembly line, have a defined sequence of actions performed by the robots on the objects being assmbled. In-space assembly is no different – all assembly projects require a starting point and a defined method that even a fully autonomous robot uses to determine its next task.
Autonomy
In order for a robot to behave autonomously, a VICON motion capture display (below) is used to track robotic components in 3D space. This information, combined with structure images, joint images, and actuation response, is used to create a combined vector. This vector leads into multiple iterations of convolutional layers and pooling layers until a fully connected layer is formed. This layer is used to define the error classifiers, including component pose errors, component error status indicators, and joint error status indicators. After determining error, the robot must take action independent of human input.
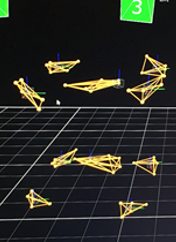
Serviceability
Once infrastructure has been established in orbit or beyond, focus will shift from constructing physical structures to maintaining them.
The James Webb Space Telescope (JWST) is designed to be deployable and non-serviceable due to its intended distance from Earth. The resulting costs associated with this decision prompted Congress to mandate that all future space observatories have a plan for maintenance and service, similar to the Hubble Space Telescope, which was serviced multiple times along its ongoing lifespan. The reason is purely economical – if a crucial instrument is maintained, its increased lifespan often negates the need for a replacement, especially if the unit’s capabilities can be upgraded through the same servicing mechanism.
Robots that construct vital space infrastructure should be capable of the dual purpose of maintaining these structures, deconstructing portions as necessary, replacing components, and reassembling. Robots should also be independently capable of detecting, through machine vision or by other means, whether or not a structure needs repair. (Below: An LSMS completing construction of a lunar base.)
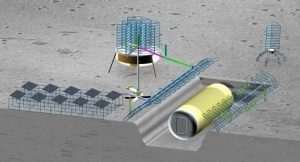
Servicability also means that the robots should be able to maintain themselves and preserve their own useful operation. The Spirit and Opportunity Mars Exploration Rovers (MERs) famously outlasted their primary 90-day mission by many years, but ultimately failed because of environmental factors that would have been survivable with collaborative help. Large format assembly robots should be modular in that they can replace their own damaged components or that of their teammates. They should be scalable, such that productivity increases with an increased number of robots. They should possess a wide variety of end effectors, allowing any individual robot to pick up a tool to perform a specific task.
Toward the future
The future of the human race in space is dependent on our ability to economically construct permanent infrastructure in low earth orbit and beyond. Ideally, this process will include in-situ resource utilization (ISRU) and logically must include robotic assembly, as the void of space is far too dangerous and costly to operate humans in, while robots can perform a ceaseless function with far greater accuracy.
The FASER Lab intends to be on the forefront of new assembly technologies and methods, particularly in the areas of collaborative and autonomous/intelligent assembly. The vast distances from earth that these proposed systems will work in make live control or teleoperation infeasible, meaning that robots will have to coordinate their own actions, including detecting and compensating for errors.
The images to the left and right of this text illustrate early NASA concept art for sustainable space infrastructure: A lunar colony with a mass accelerator orbital launch system and a Stanford torus style space colony (both below). Close examination of the primary features of these systems show applications in which Robots, even performing simple repeatable tasks, would be immeasurably useful. A mass accelerator, for instance, is built out of many identical magnetic core modules. A robotic system could transport these modules, arrange them, and attach them together all without human assistance in environments that no human could withstand without copious and performance -limiting environmental protection.
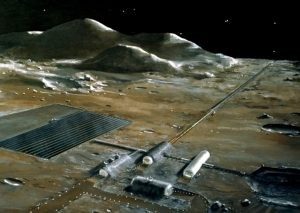
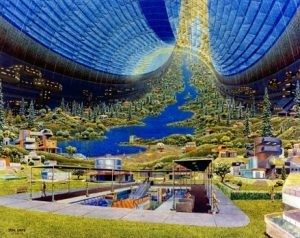
In the near term, robotic assembly methods developed at NASA Langley Research Center and Dr. Komendera’s FASER Lab could lead to the construction of persistent orbital power generation (solar) platforms, solar electric tugs/interplanetary transit vehicles, and a new generation of robotic space station.